First patient successfully operated with 3D printed hip socket manufactured in Factory-in-a-box point of care system powered by Meticuly at Siriraj Hospital
- chetarpa yipyintum
- Apr 3
- 3 min read
Bangkok, Thailand, April 2nd 2025 - OSS3O, a joint venture between Meticuly and Mr. T Thirakomen of MK Group, and Siriraj Hospital hold press conference to announce first patient successfully operated with 3D printed titanium implant manufactured at OSS3O, a pioneering "Factory-in-a-Box" point-of-care facility powered by Meticuly. The event is officiated by Ms Supamas Isarabhakdi, Minister of Higher Education, Science, Research and Innovation.
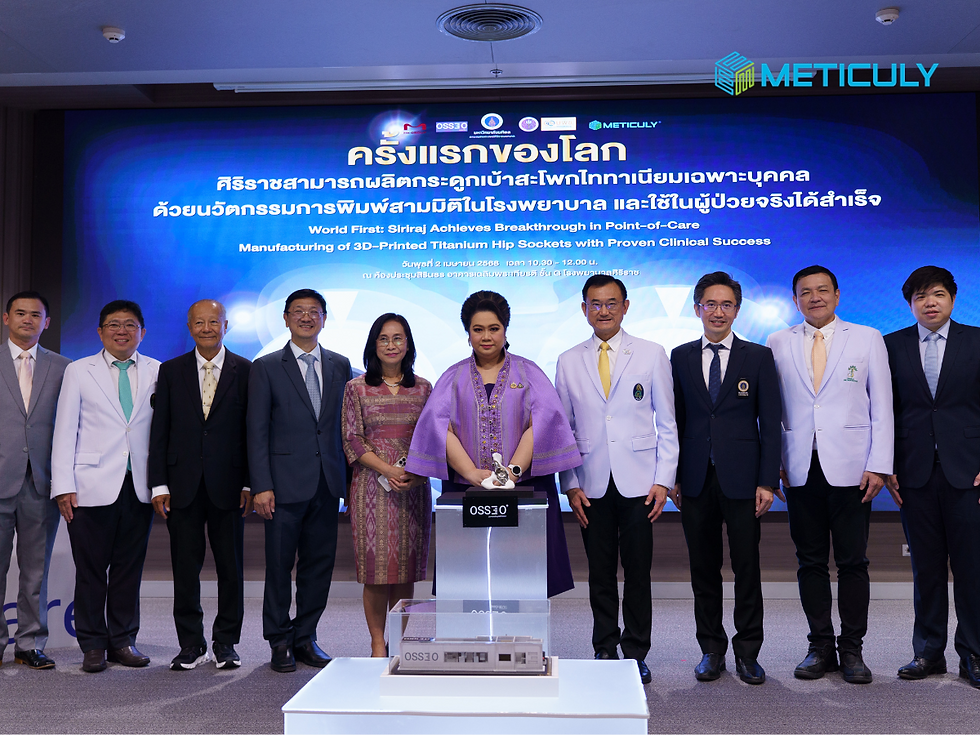
A collaborative effort for advanced patient care
Since the signing of the MOU in July 2024, Meticuly and its partners have joined forces and successfully established a state-of-the-art manufacturing facility, fully equipped with advanced 3D printing technology. This facility not only produces surgical guides, biomodels, and prototypes to enhance pre-surgical planning but also features a titanium 3D printer capable of manufacturing patient-specific implants.
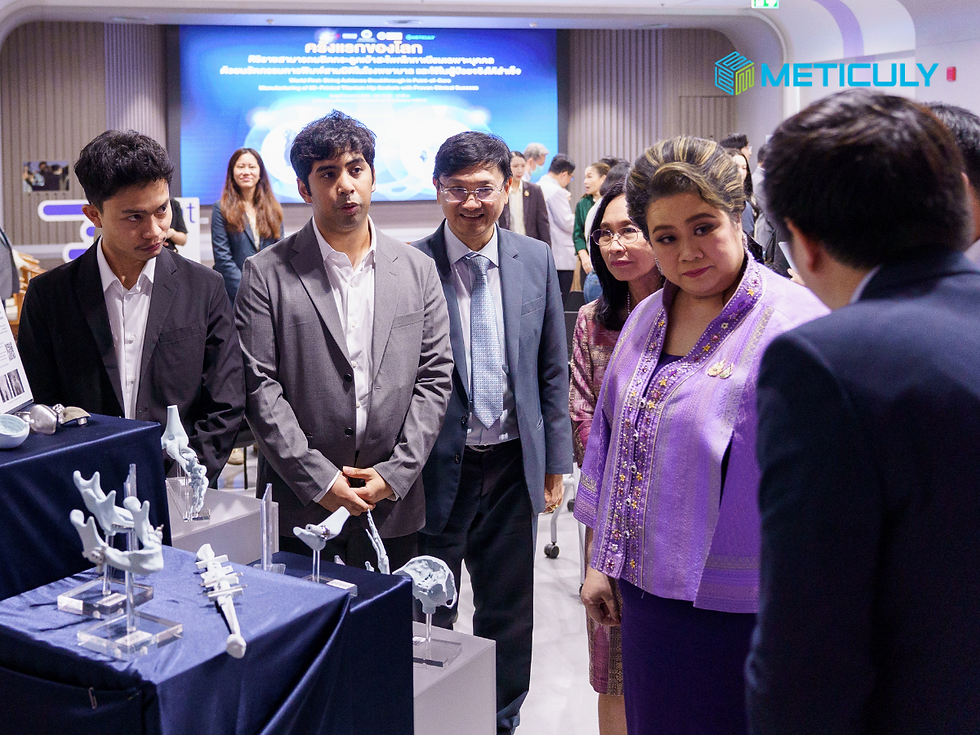
Factory-in-a-Box: A World-First Innovation at Point-of-care
Strategically located next to the operating theatre, OSS3O represents a world-first: a "Factory-in-a-Box" point-of-care manufacturing system. This innovative concept, developed by Meticuly, utilises an advanced modular system, integrating AI and automation to condense a large-scale implant manufacturing facility into a compact, container-sized unit. This enables on-site, real-time collaboration between surgeons and engineers, significantly accelerating and enhancing the production of personalised medical devices.

OSS3O is designed to support the treatment needs of over 300 patients annually at Siriraj Hospital. By integrating Meticuly’s cloud-based design technology with its proprietary manufacturing systems, this facility at Siriaj Hospital represents the first prototype of Meticuly’s satellite manufacturing model—pioneering a new era of personalised medical solutions.

Transforming Patient Outcomes
The first patient to receive a 3D-printed titanium implant produced at the OSS3O facility, demonstrating the effectiveness of Meticuly's point-of-care system. The procedure was an acetabular reconstruction, a complex procedure to restore hip joint function. It took only 7 days from design finalisation to the final 3D printed implant, sterile and ready for operation.
Quotes from Key Stakeholders
“I operated on Mr Boonrob in the beginning of March. The procedure was successful, and the patient is now on their path to recovery. At Siriraj Hospital, we treat many patients who present with similar conditions as this patient. The challenge with these kind of hip revision surgeries is that a significant portion of the hip socket have degraded, meaning that standard sized implants can not be used. ” said Prof. Dr. Keerati Charoencholwanich, M.D., operating surgeon and Head of the Department of Orthopaedic Surgery.
Prof. Dr. Apichat Asavamongkolkul, M.D., Dean of the Faculty of Medicine at Siriraj Hospital, emphasised the impact of this advancement: “With the 3D-printing capabilities on-site, we will be able to treat even more patients with a patient-specific solution. I have colleagues from oculoplastic, oral and maxillofacial, orthopedic and plastic surgery specialties waiting to utilise the in-house printed products for their patients. Particularly in complex and time-critical indications, the use of patient-specific implants will lead to reduced surgery time, less blood loss, lower complication rates and better patient outcomes. This innovation is going to leverage Siriraj to a new level of healthcare excellence.”
Asst. Prof. Dr. Chedtha Puncreobutr, Meticuly CTO and OSS3O Project Lead, concluded: “We are incredibly proud to bring this groundbreaking innovation to life in one of Asia's leading medical institutions. This achievement marks a major milestone, but it is only the beginning. Our vision is to revolutionise healthcare by empowering hospitals around the world with an accessible, straightforward solution for point-of-care titanium 3D printing, ultimately changing the way we think about personalised patient care. Bringing our technology to the point-of-care has the potential to significantly reduce wait times, improve surgical outcomes, and enhance recovery, ultimately leading to better quality of life for those in need.”
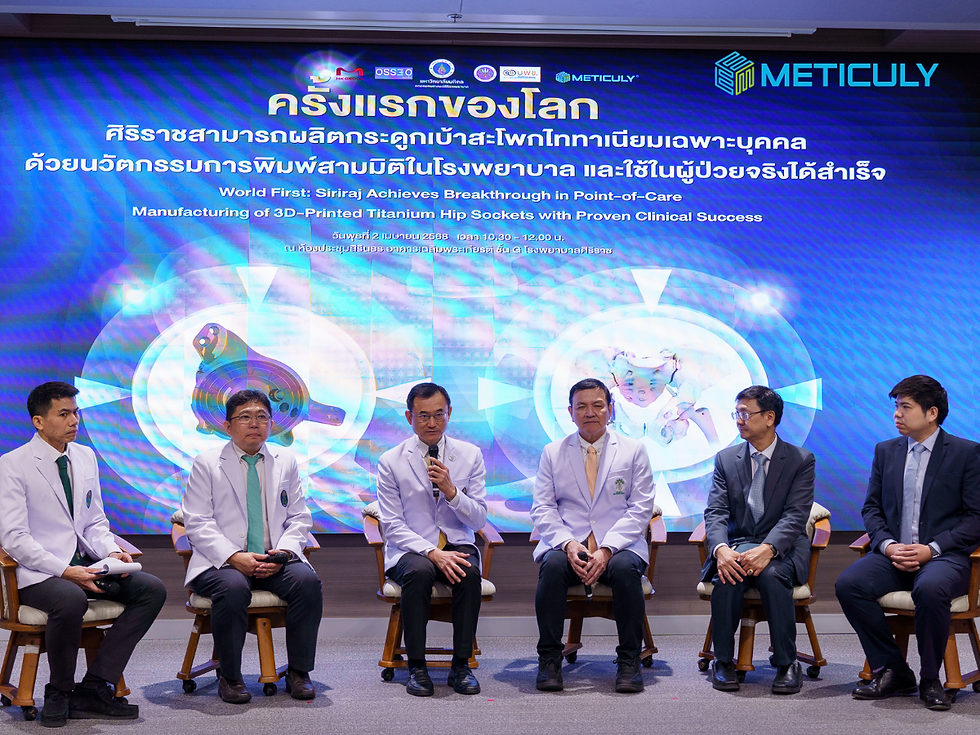
Meticuly: Leading the Way in Personalised Healthcare
As Meticuly continues to expand globally with its patient-specific implants on demand, the company’s point-of-care solution, exemplified by the "Factory-in-a-Box" model, is paving the way for a new future of manufacturing. This brings advanced, patient-specific technology closer to those who need it most, transforming the delivery of personalised medical care.
Contact us at global@meticuly.com for more information.
Comments